Housebuilding ain’t broke, so should we fix it?
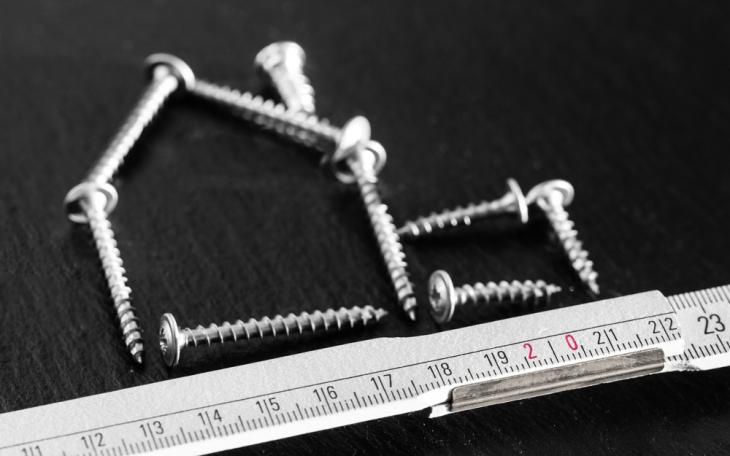
By Laura Sears
The earliest recorded properties built by bricks were found in Jericho, Turkey, and date back to around 5,000BC. Fast-forward over 7,000 years, and we’re still predominantly using this method to build homes.
“Traditional” bricks and mortar build is largely seen as the development method of choice, though there are many companies chomping at the bit to revolutionise the housebuilding industry, especially with the government pledging hundreds of thousands of new much-needed homes – particularly affordable ones – each year.
New players in the market, such as airspace developers Apex, are championing Modern Methods of Construction (MMC) to bring large quantities of homes forward quickly. Even traditional housebuilders such as Countryside are looking to invest more into MMC. A poll conducted at the RESI Conference earlier this month seemed overwhelmingly in favour of MMC, predicting that over 25% of new homes will be built off-site in the future.
But if bricks and mortar have worked for thousands of years, why fix something which doesn’t necessarily need fixing? The implications of MMC, particularly for residential development, are significant.
Modular construction is widely accepted in the commercial sector, with schools, leisure centres etc often built off-site, and accounts for about 15% of all new builds in Japan. The key USP is applicable to housebuilding too: volume.
Off-site manufacturing of homes, much like cars, can be processed in factories in panels and pods on a mass scale, controlling the quality and consistency of the product. These are built to be installed later, which reduces the need for construction at the site itself and in turn reduces labour costs, as well as time spent disturbing neighbours. 75% of the whole cost is locked down in the manufacturing stage, and is easier to make continuous and speedy improvements – as well as being more sustainable – which has a knock-on effect in the base cost of the homes and consequently enables more affordable product to come to market.
The difficulty comes further down the line, with sales. A Home Group & YouGov survey showed 52% of people wouldn’t choose a modular home (around 70% of respondents associated the ‘modular’ home with shipping container homes) because they were nervous about the quality of the product, however only 11% of those questioned actually understood what the term modular meant properly.
Grenfell has brought the question of quality and materials into sharp focus, and it’s understandable that people will be nervous about something new. But the tragedy also made the industry take a frank look at its own methods as well, with stricter regulations and better warranties now often in place.
COVID-19 has put the property market firmly in the spotlight: we’re using our homes in different ways; as our workplaces, our leisure spaces as well as places to relax. MMC makes it easy to add additions to our homes like loft conversions, external pods for home offices or rear extensions.
MMC isn’t an either/or – it’s an accelerator to help speed up the housebuilding process in a cost-effective way. Granted, you can’t just set up a modular homes factory anywhere – you have to be strategic about the types of homes you’ll be building and where, but if the only way to get real scale is to find standardised ways across the whole industry, it’s likely off-site construction will become more mainstream, just as the panel at RESI suggested: might we even get to a point where traditional build is seen as ‘quaint’ and even a bit ‘out-there’?